미국 UAM 기체 제작사 조비 R&D센터 가보니
중형 SUV 무게에 1회 충전으로 최대 241㎞ 비행
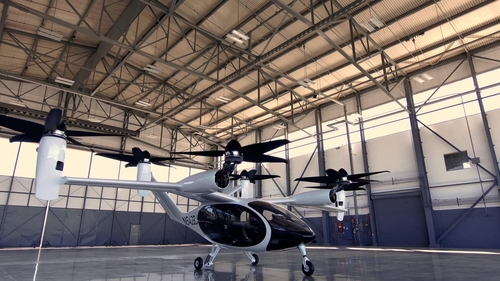
(마리나[미 캘리포니아]=연합뉴스) 정성호 특파원 = 미국 실리콘밸리에서 차로 1시간 20분을 남쪽으로 달려 도착한 마리나 지방공항 한쪽에는 창고처럼 단조롭게 생긴 건물이 몇 동 세워져 있었다.
공항 활주로 바로 옆에 위치한 이 투박한 건물은 도시 상공을 날며 승객을 실어나를 미래 교통수단인 UAM(Urban Air Mobility, 도심항공교통) 항공기를 제조하는 미 전기항공기 업체 조비 에이비에이션의 연구개발(R&D) 센터다.
조비는 UAM으로 쓰일 수직 이착륙 비행체(eVTOL) 개발에서 가장 앞서 있는 기술 업체로 평가된다. 이 R&D센터는 그런 첨단기술의 산실이자, 그 첨단기술을 더 앞으로 진전시키고 있는 사령탑인 셈이다.
건물 한 동에 마련된 격납고에는 조비가 개발한 eVTOL 'S4'와 헬리콥터 3대가 세워져 있었다. 기자가 방문한 날은 기상 등의 문제로 시험 비행을 하지 않았다.
조비의 항공우주 엔지니어 에릭 라슨은 "S4가 비행하면 이를 추적하며 모니터링해야 하는데 속도가 빨라 헬리콥터 1대로는 이를 따라갈 수 없기 때문에 항상 헬리콥터 2대를 띄워 모니터링한다"고 설명했다.
S4는 무게가 중형 스포츠유틸리티차(SUV) 수준인 5천파운드(약 2천270㎏) 이하이면서 최대 4명의 승객을 태우고 시속 320㎞로 순항운행할 수 있다.
1회 충전으로 최대 241㎞를 간다. 지상 300∼600m 상공에서 날아다닌다.
이착륙은 헬리콥터처럼 수직으로 오르내리지만, 일단 하늘에 올라가면 날개의 양력을 이용해 비행한다. 이렇게 하면 에너지 효율을 높일 수 있기 때문이다.
라슨은 "이를 위해 모든 프로펠러가 최대 90도 방향이 전환되도록 설계됐다"며 "날개의 힘을 이용하지 않고 프로펠러만 이용해 제자리에 떠 있는 시간이 길수록 배터리가 많이 소모돼 비행 거리는 줄어든다"고 설명했다.
S4는 특히 '분산 전기 추진'(distributed electric propulsion) 시스템을 채택해 항공기에서 가장 중요한 안전성을 높였다. 분산 추진이란 헬리콥터처럼 단일 추진체에 의존하는 대신 총 6개의 프로펠러를 기체 곳곳에 분산 배치한 것이다.
조비의 파트너십·전략 부문장 저스틴 랭은 "새 기체를 설계할 때 최적의 성능을 발휘하는 것뿐 아니라 항공 모빌리티가 우리의 일상의 한 부분이 되지 못하도록 가로막는 모든 단점을 해소하는 데 목적을 뒀다"고 설명했다.
그러면서 헬리콥터를 예로 들었다. 헬리콥터는 많은 장점에도 불구하고 기체 구조상 안전성을 위협하는 결함 요소가 많고, 소음이 심각한 데다, 항공기로서는 상대적으로 느리고 운영 비용이 비싸다는 것이다.
랭 부문장은 "안전성과 정숙성, 그리고 실용성이 우리 기체 설계의 목표였다"고 말했다.
안전성 면에서는 헬기보다 가볍고 단순한 전기모터를 채택한 프로펠러를 만든 뒤 이를 6곳에 분산해 배치하고, 여기에 보태 보조 모터와 배터리를 추가로 달았다.
어떤 모터나 배터리가 문제를 일으키면 이 보조 모터와 배터리가 그 역할을 대신해 안전하게 착륙할 때까지 계속 가동할 수 있도록 한 것이다.
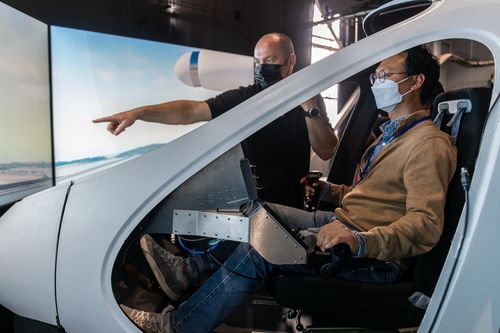
랭 부문장은 또 "소음과 관련해서도 중대한 혁신을 이뤘다"며 "왜냐하면 UAM이 우리 일상에 영향을 끼치려면, 이 기체를 사람들이 거주하고 일하는 곳에 가깝게 가져갈 필요가 있다는 것을 알았기 때문"이라고 말했다.
전기모터는 조용하지만 프로펠러의 크기나 속도로 인해 여전히 큰 소음이 발생했다. 하지만 조비는 S4의 소음을 최고 65데시벨(㏈)로 낮췄다. 이는 고속도로를 달리는 자동차에서 나는 소음 수준이다.
또 S4가 상공을 날 때 지상에서 들리는 소음은 도서관 수준인 40데시벨로 낮아진다.
실용성 제고를 위해선 전기 파워트레인 혁신에 중점을 뒀다. 그 결과 테슬라 모델3에 들어간 전기모터보다 3배의 추진력, 6배의 포트 밀도를 지닌 모터를 개발했고 이는 1회 충전으로 241㎞를 가는 성능으로 이어졌다고 랭 부문장은 설명했다.
이 격납고 건물 맞은편에는 S4 제조공장이 있다. S4가 상용화될 때까지는 아직도 2년 이상 남아 있기 때문에 아직 대량생산이 이뤄지는 단계는 아니다. 그보다는 미국 항공 규제 당국인 미 연방항공국(FAA)의 인증을 통과하기 위한 각종 시험 비행과 R&D에 초점이 맞춰져 있다.
본사가 있는 캘리포니아 샌칼로스 사옥, 전기 파워트레인과 배터리팩을 생산하는 샌타크루즈 사옥과 달리 마리나 사옥은 앞으로 기체를 생산할 핵심기지가 될 예정이다.
현재는 시험생산 단계로 연간 30대를 만드는 수준이지만 목표한 대로 2024년 미국에서 UAM이 상용화되면 1단계로 연간 생산량을 200∼400대로 늘리고, 2단계 때는 연간 수천 대를 제조한다는 목표다.
S4는 부품과 부품이 연결되는 접합 부위에만 금속을 쓰고, 나머지 기체의 98%가 첨단 소재인 탄소섬유로 만들어졌다. 동체는 물론 프로펠러의 날개나 꼬리 날개 등도 모두 탄소섬유로 제작된다.
탄소섬유는 알루미늄보다 가벼우면서도 철보다 강한 강도와 높은 탄성을 지녀 항공기 동체나 건축 내장재, 고가의 자동차·자전거 등에 쓰이는 값비싼 소재다.
이 때문에 공장 내부의 풍경은 여느 완성차 업체의 생산설비처럼 컨베이어벨트가 바쁘게 돌아가는 모습이기보다는 정적인 느낌이었다. 탄소섬유 소재를 부품의 형태와 크기대로 맞춰 로봇팔을 이용하거나 사람이 직접 가위로 재단하고 이를 여러 겹 이어붙인 뒤 10기압의 고압 또는 진공의 힘을 이용해 압착하는 게 주요 제조 공정이다.
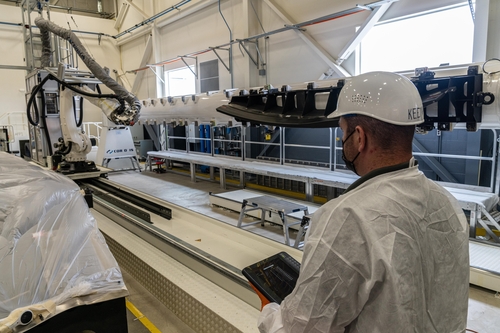
가장 큰 부품은 역시 날개로, 이를 만들기 위한 금형의 크기는 폭이 10m를 넘는다. 이런 큰 부품은 금형 옆에 설치된 10m 길이의 커다란 원통형 로봇팔이 가공하고 절단한다.
프로펠러를 구성하는 날개(blade)도 탄소섬유로 만드는데 무게는 영업비밀이라고 라슨은 말했다. 기체 1기당 이 날개는 모두 30개가 들어간다. 기자들이 손으로 들어보고 내놓은 추정치는 1㎏ 미만이었다.
이렇게 기체의 대부분이 탄소섬유로 이뤄지다 보니 번개에 취약해서 이에 대응할 수 있도록 꼬리 부품에는 구리 매트를 코팅한다.
라슨은 "우리 기체도 FAA의 인증을 받지만 이 생산시설과 환경 관리 역시 FAA로부터 인증을 받고 각종 생산 공정에 대한 기록을 남겨야 하는 등 엄격한 관리를 받는다"고 말했다.
조비가 생산한 항공기는 국내에서 이 사업을 추진 중인 SK텔레콤을 통해 이르면 2025년부터 국내에서도 운항할 예정이다.
sisyphe@yna.co.kr
(끝)
<저작권자(c) 연합뉴스, 무단 전재-재배포 금지>
관련뉴스